When Bosch in Germany delivers 50 sensor housings in 5 days, and Johnson & Johnson in the US clones surgical instrument prototypes in silicone molds – silicone replica molding (vacuum injection molding) is disrupting the logic of low-volume production as a “flexible steel mold”. With only 10% of the cost and 1/3 of the cycle time of opening a steel mold, this process has become a strategic choice for R&D departments around the world.
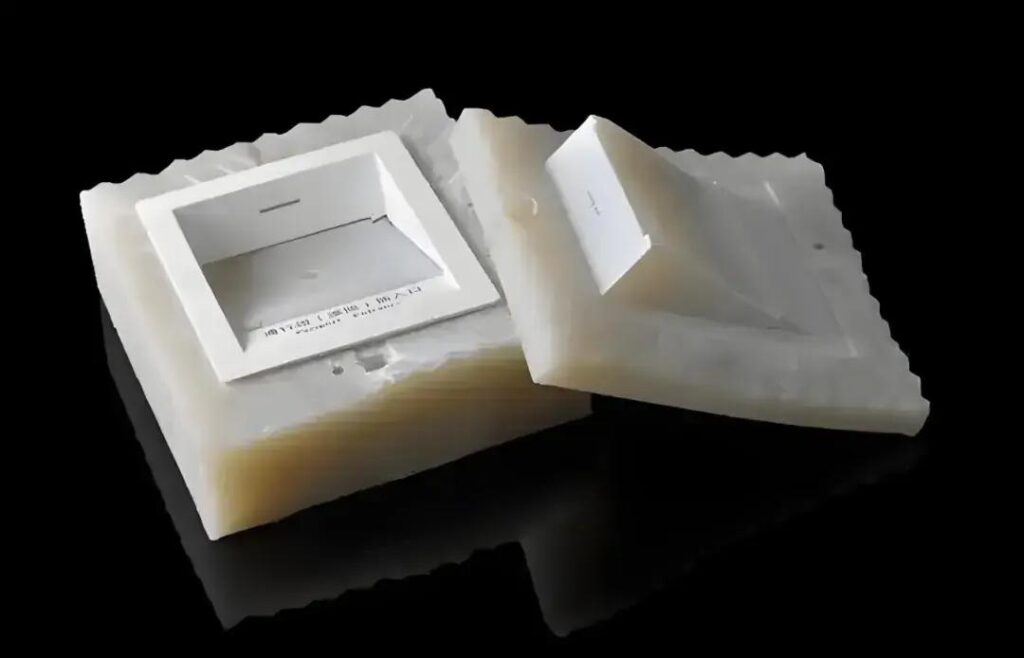
Core process analysis: four steps to realize precision replication
1. Prototyping: the starting point of physicalization in the digital world
Industrial-grade prototype standards:
SLA light-curing: layer thickness 0.05mm → surface roughness Ra≤1.6μm (for precision gears)14
CNC aluminum alloy machining: positioning accuracy ±0.01mm (preferred for automotive structural parts)
Lessons Learned from the Blood and Tears of German Enterprises:
A medical device maker adopts FDM to print prototypes → layer pattern replica to silicone molds → accuracy of the chamber runner is out of precision → failure in fluid testing
2. Silicone molds: nanoscale replication in a vacuum environment
Golden parameter system:
makings | Hardness (Shore A) | tear strength | Applicable Scenarios |
---|---|---|---|
Food Grade Silicone | 25-30 | 35kN/m | medical equipment |
high-temperature silicone | 40-45 | 50kN/m | Engine compartment parts |
Industrial Grade Silicone | 60-65 | 45kN/m | Consumer electronics housings |
Vacuum defoaming life and death line:
▶ Air bubbles > 0.3mm → automotive gear breaking load ↓ 35%
▶ German double vacuum program: -0.95bar pre-foaming + -0.9bar mold cavity vacuum → defect rate to 0.05%.

3. Vacuum injection molding: precise regulation of material science
Polyurethane performance equation:
Tensile strength (MPa) = Curing temperature (℃) × 0.25 + Holding time (min) × 0.18
Toyota Japan case:
▶ Curing at 80°C for 45 minutes → PUR hardness up to 85 Shore A → Replacement of injection-molded ABS
4. Post-processing: Transformation from blanks to fine products
Micron Surgery for Fly Edge Removal:
Laser Cutting Accuracy 0.1mm → Avoiding Stress Concentration on Glass Fiber Reinforced Parts
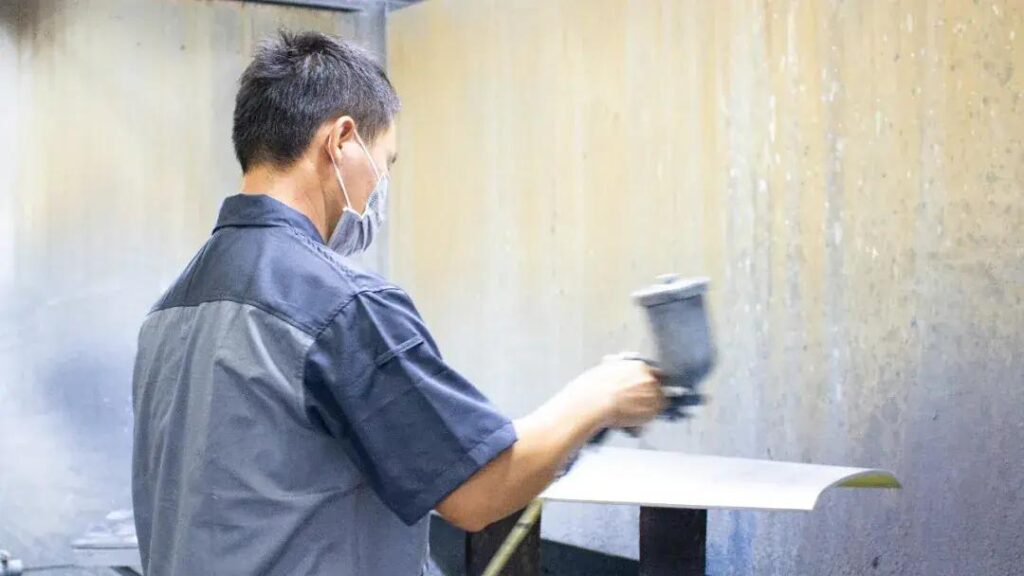
Coating adhesion code:
▶ Plasma treatment improves surface energy to 72 dyn/cm → 300% better adhesion with spray paint.
Disruptive Advantage: The Golden Rule of Low Volume Production
The Cost-Effective Nuclear Explosion Formula
Silicone mold cost per piece = (Mold cost/1000) × 0.15
Economic inflection point model:
Number (N) | Optimal process | Cost Comparison Steel Mold |
---|---|---|
N≤20 | 3D printing | basically flat |
20<N<100 | Silicone replica mold | Only 35% |
N>100 | Aluminum Mold Low Pressure Infusion | 60% |
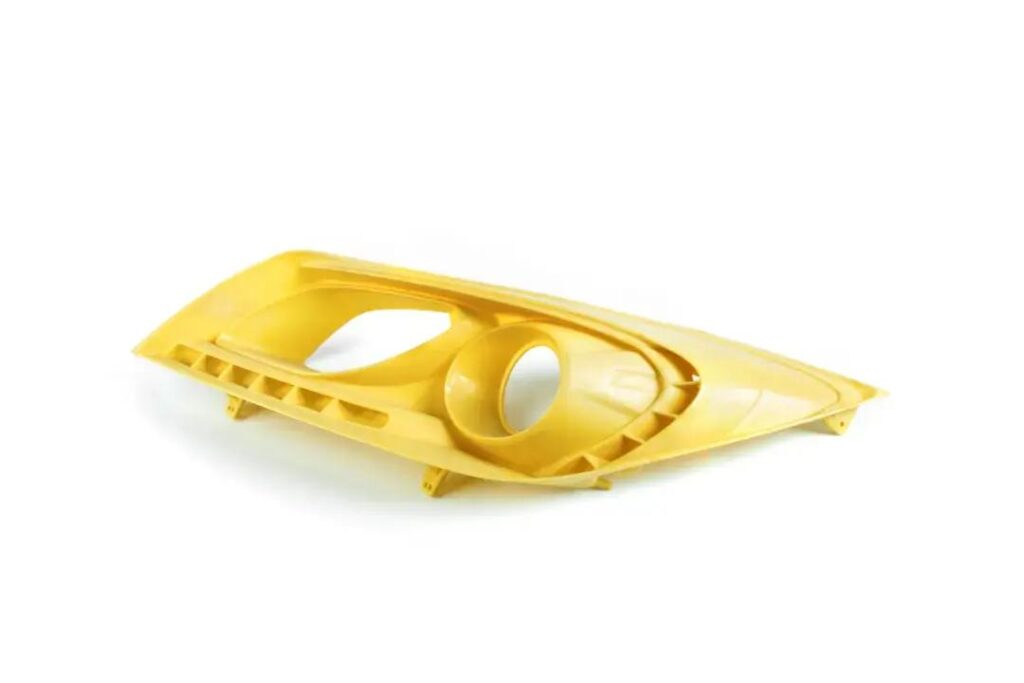
Speed crushes traditional craftsmanship
Mercedes-Benz door panel case:
Steel mold: 28 days to open the mold + 5 days for trial production → 33 days total cycle time
Silicone re-molding: 3 days for prototype + 2 days for mold + 2 days for injection → 7 days total cycle time
Balancing precision and function
Medical-grade replica standards:
▶ Microfluidic structure replication accuracy ±0.05mm (compliant with ISO 13485)
▶ Medtronic insulin pumps from the U.S.: Passed 200 assembly tests
Industry Breakout: Practical Maps of the World’s Top Companies
Automotive components: Life and death verification before crash tests
Tesla Battery Pack Mount:
Silicone re-molded 50 pieces → Vibration test exposed resonance points
Optimized reinforcement design → Avoided 8-12Hz dangerous frequencies
Saved $120,0004 in steel mold modification fees
Medical Devices: Avoiding Million Dollar Certification Risks
Johnson & Johnson Joint Surgical Guides:
Medical-grade LSR silicone replica → passed ISO 10993-5 cytotoxicity test
6 weeks faster than open mold certification → captured FDA priority approval
Consumer Electronics: Limited Edition Profit Engine
Sony PS6 Limited Edition Grip:
200 sets of silicone replicas → customized gradient plating coating
300% increase in unit price → $2M in fan economic gains
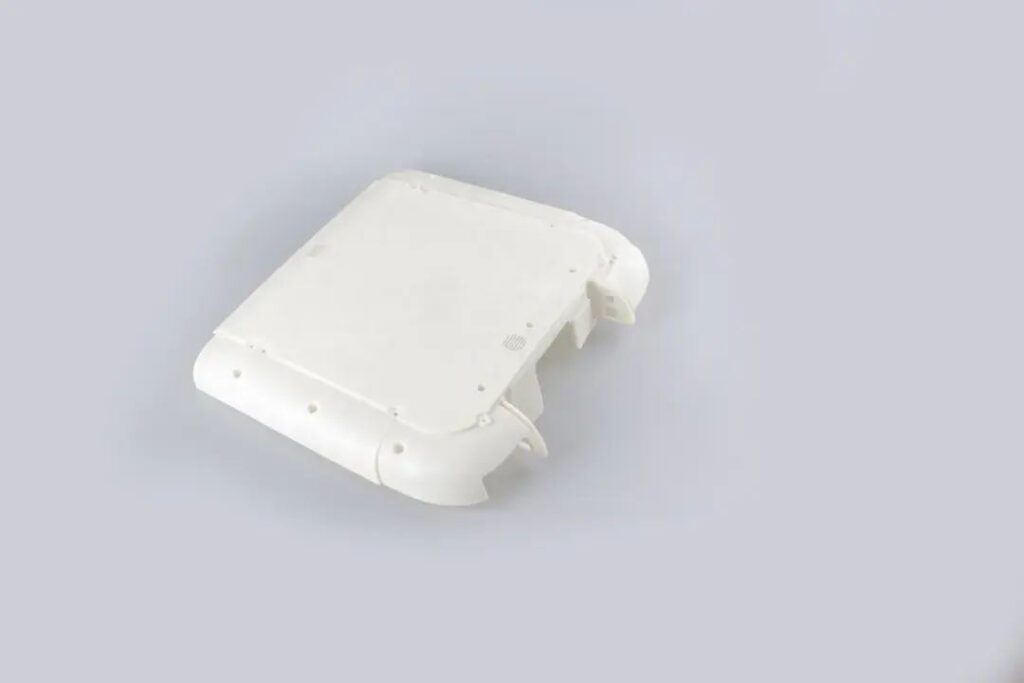
Technical minefield: 5 high-cost traps and cracking solutions
Shrinkage out of control
Disaster case: drone shell shrinks by 0.25% → snap assembly fails
Bayer solution: add 7% fiberglass → shrinkage reduced to 0.02%.
Homogeneous sticky mold predicament
Breakthrough technology:
▶ ABS molds instead of silicone molds → Solve liquid silicone sticking problem2
▶ Nano mold release agent coating → Release force ↓40%.
Temperature-sensitive trap
Japanese standard: environment >50℃ → PU parts deformation rate ↑15%
Mitsubishi countermeasure: high-temperature-resistant resin EPX 82 → temperature resistance exceeds 120℃.
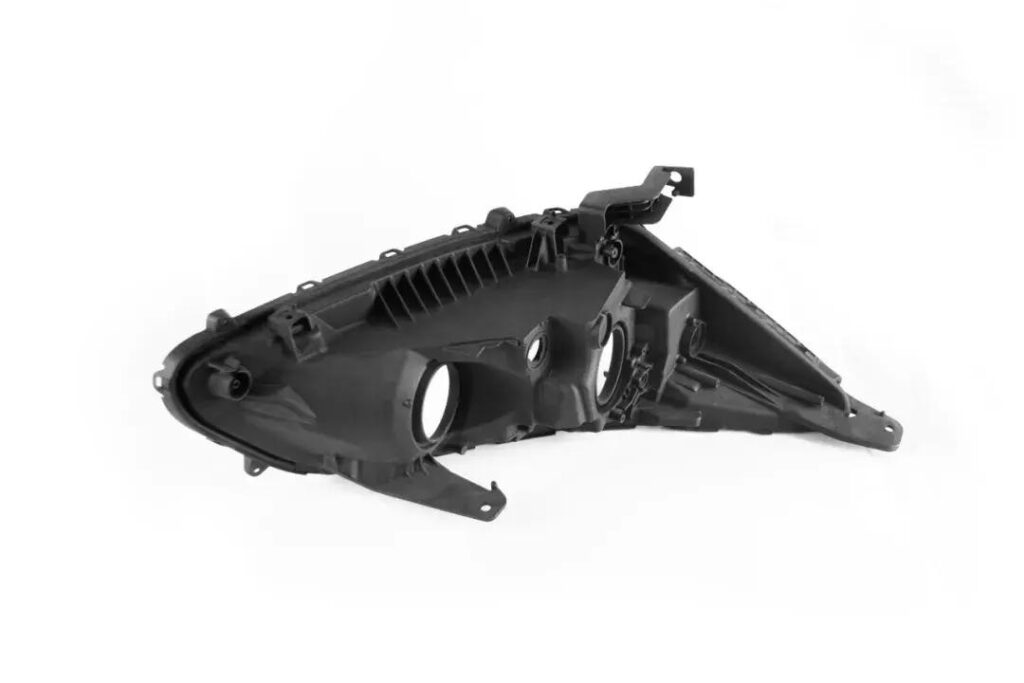
Detailed reproduction distortion
Optical parts solution path:
mold nano-polishing → surface Ra ≤ 0.01μm
+ Vacuum coating → Transparency >99%.
Mold life decay
Sika’s secret:
▶ Add 3% ceramic particles to the silicone → Mold life exceeds 30 die times.
Future Battlefield: Intelligence and Sustainability Revolution
AI-driven process evolution
Israel’s NanoFlow system:
▶ Machine vision detects air bubbles in real time → Dynamic adjustment of vacuum parameters
▶ Yield increased to 99.2%.
A New Era of Green Manufacturing
WACKER Bio-based Silicone, Germany:
Carbon emissions ↓ 55% + Degradability > 90%
BMW 2026 Full Switchover Plan
🌟 Conclusion: Reshaping the Manufacturing Boundary between Flexibility and Precision
Silicone remolding is not only technology, but also a strategic bridge between innovation and the market. When polyurethane precisely fills 0.02mm microtextures in a vacuum, when medical silicone cures life-support cavities in a thermostat – these seemingly flexible processes are rigidly defining the future of low-volume manufacturing.