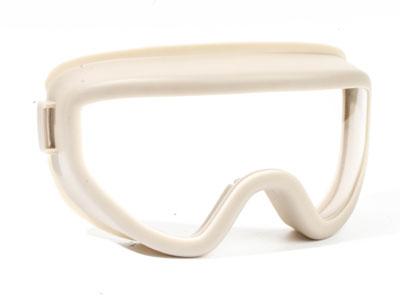
Case Details
Product Name: Silicone molding processing soft rubber diving goggles
Industry/Classification: Marine
Processing method: CNC metal processing
Material used: soft plastic
Maximum precision: 0.1mm Production cycle: 5
Product size: 18cm*7.25cm*6cm
Post-processing: deburring
Case Introduction
Silicone compound mold processing process:
1.Manufacture prototype: According to the 3D drawing supplied by the customer, the prototype is manufactured through CNC machining, SLA laser rapid prototyping or 3D printing.
2. Pouring silicone mold: After making the prototype, make the mold frame, fix the prototype, pour the silicone, and after 8 hours of drying, open the mold and take out the prototype, the silicone mold manufacturing is finished.
3. Injection: inject the liquid gum material into the silicone mold, in the 60 ° – 70 ° constant temperature box for 30-60 minutes after curing, can be removed from the mold, if necessary, in the 70 ° – 80 ° constant temperature box for 2-3 hours of the second curing. Generally under normal circumstances silicone mold life is 15-20 times.
The characteristics of small batch silicone re-molding hand plate:
1. Silicone mold does not deform, does not shrink; high temperature resistance, mold molding can be used repeatedly after molding; for product imitation to provide convenience;
2. Silicone molds are inexpensive, short manufacturing cycle, and can prevent unnecessary loss before opening the mold.
This case is a diving goggle frame made using silicone re-molding process, using soft rubber material for re-molding.


