In the top manufacturing labs in Europe and the United States, a Rapid Prototyping sample with a perfect surface treatment often determines whether a new product can receive millions of dollars in venture capital. When engineers take the Apple MacBook case prototype out of the CNC machine, there is a magic called Surface Finishing between the gray aluminum billet and the final brushed space gray metal effect. This is not only a matter of aesthetics, but also about the credibility of the product’s texture, the accuracy of functional testing, and the user’s first value judgment.
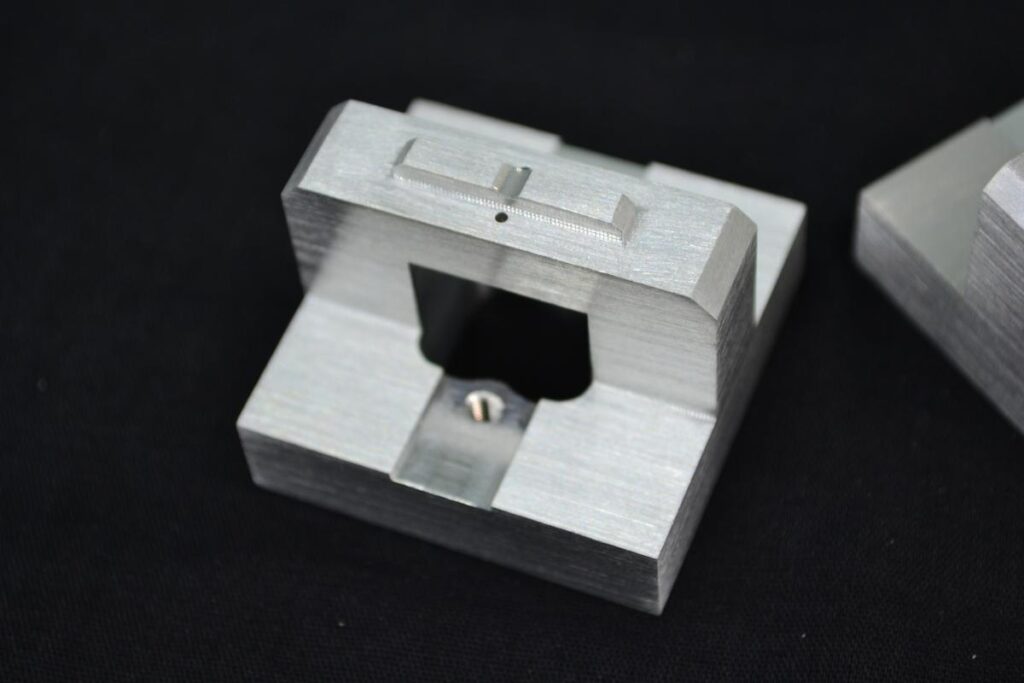
Why Surface Finishing is the “Second Life” of Rapid Prototyping?
Rapid prototyping is just born from CNC machining or 3D printing, often with knife lines, lamination lines, burrs and other “birth traces”. Surface treatment is not just cosmetic surgery, it is the key to giving prototypes a triple soul:
Functional simulation: sandblasted medical instrument handles are non-slip ≈ mass-produced parts
User perception test: soft-touch paint spraying on automotive interior parts directly affects user experience feedback
Technical validation: polishing accuracy of optical parts determines the reliability of light transmission rate test data
Data from Bosch Germany reveals that developed prototypes without professional surface treatment have a 67% poor user rating in crowdfunding tests. This explains why Silicon Valley companies are willing to invest 15-30% of their prototype budget in surface finishing.
Rapid Prototyping Surface Finishing Process Panorama: Core Technology Analysis and Application Scenarios
1. Spray Painting: The Balancing Act of Covering and Aesthetics
Technology core: through the principle of electrostatic adsorption, atomized paint evenly wraps around the surface of the prototype.
Innovative breakthroughs:
Soft Touch: adding elastic resins to achieve skin-like touch (keyboards, grips).
Metallic Paint: paint mixed with aluminum powder to simulate the appearance of metal at a low cost.
Benchmarking case:
Jabil adopted a dual-coating spraying process for the prototype of a Dyson vacuum cleaner: a conductive base coat and a matte rubber paint, which simultaneously solved the problem of Eco-friendly and aesthetically pleasing surface. Jabil’s dual-coating process for a Dyson vacuum cleaner prototype: conductive base coat + matte rubberized finish, solving both EMI shielding and grip comfort pain points.
2. Sandblasting: a micro-engraving artist
Parametric precision control:
Aggregate type | Grain size | surface effect | Applicable Scenarios |
---|---|---|---|
glass bead | 80-120 | even matt | Medical Equipment 🌡️ |
aluminum oxide | 60-100 | Fine texture | Electronic product shells |
silicon carbide | 36-60 | heavily frosted | tool handle |
Failure Alert: A prototype of a 2022 SpaceX fuel valve ruptured in hydraulic testing due to 0.3mm wall thinning from excessive sandblasting. Controlling blast time to <8 minutes is key!
3. Plating: putting metal armor on plastics
Material Prohibition List:
▶ PC plastics plated directly in water = peeling off of the plating layer (need to spray primer first)
▶ POM plastics need to be etched before plating.
4. Anodizing: Native Armor for Aluminum
Medical grade anodizing model: Johnson & Johnson orthopedic joint prototypes use hard anodizing, film thickness 50μm↑, hardness ≈ sapphire
Color Black Technology:
A,、Aluminum billet –> Electrolytic coloring –> Voltage control –> 15V: Champagne gold
B、 Aluminum billet –> Electrolytic coloring –> Voltage control –> 20V: Titanium air grey
C、 Aluminum billet –> Electrolytic coloring –> Voltage control –> 25V: Obsidian black
The influence of electrolysis voltage on the oxidation color of aluminum alloy.
5. Laser Engraving: A mark that never disappears
Translucent engraving techniques:
Spray black matte paint on the bottom layer
Spray white paint on the surface layer
Laser ablation of the white layer to reveal the black background
→ Create a backlit button effect (automotive center panel prototype)
Precision Limit Warning: Curved surface engraving deformation rate of> 12%, plane engraving area> 100 x 100mm need to be spliced
6. Vapor Smoothing (Vapor Smoothing): The Savior of 3D Printing
Chemical reaction equation:
C8H8 (PA12 powder) + ethyl acetate → surface molecular chain reorganization
Disruptive Advantage:
Processing Time: 3 minutes vs. 30 minutes for manual polishing
Cost Reduction: 40% reduction in post-processing costs for hip models from Medical Models Inc.
Industry Application Decision Tree: The Golden Rule for Selecting Optimal Surface Processes
Medical device prototypes
Implantation testing required → Selection **Electropolishing**
Handheld instruments → **Sandblasting + rubberized lacquer dual process**
Surgical tools → **Passivation to enhance corrosion resistance**
Reference case: Medtronic surgical forceps prototype passes 168 hours of salt spray by passivation
After testing
Consumer Electronics
High-end texture: Aluminum alloy → anodizing → laser engraving (MacBook Pro process)
Cost-sensitive: Plastic → vacuum plating + UV overlay (mimics metal texture)
Fingerprint prevention solution: Matte spray with fluorine coating added
Automotive Parts
Interior parts:
3D printed texture + leather paint spray → BMW iDrive knob prototype
Engine compartment:
Aluminum die casting → hard oxidation → Tesla battery heat sink housing prototype
Future Lab: Three Game-Changing Technologies
Nanoscale plasma spraying:
ETH Zurich, Switzerland, realizes 0.1 μm ceramic coating for temperature-resistant layer of rocket engine prototype
Digital Light Synthesis (DLS):
Carbon3D introduces DLS (Digital Light Synthesis), which directly prints leathery surfaces, eliminating the need for secondary etching.
AI-driven polishing robot:
Siemens and Fanuc jointly developed AI polishing system, learning master gestures, error <±0.01mm
V. Engineer’s Choice: Surface Treatment Process Decision Matrix
This hidden algorithm decides your process recommendation when you submit your prototype requirements on the Proto Labs website:
Weight = Appearance score x 0.3 + Function score x 0.4 + Budget score x 0.2 + Delivery score x 0.1
Highly weighted decision items:
Dynamic test pieces → Prioritize sandblasting/electrolytic polishing to enhance fatigue strength
Financing roadshow samples → Electroplating/anodizing to enhance texture credibility
Small batch trial production → Silk-screen printing/padsmithing to achieve brand identity
As Tom Kelly, IDEO’s Director of Design, says, “The prototype surface is the user’s first handshake with innovation.” On Boston Scientific’s vascular stent prototype, a section just 2mm long was electrolytically polished to increase implantation success by 19%. It’s not just a triumph of technology, it’s a reverence for life.
Attachment: Comparison of Surface Process Capabilities of the World’s Top Rapid Prototyping Service Providers
service provider | Specialty Crafts | Medical Certification | Minimum Detail Accuracy |
---|---|---|---|
Protolabs | Multi-color painting + laser engraving | ISO 13485 | 0.1mm |
Xometry | Nanoscale Plating | AS9100D | 0.05mm |
Quickparts | Vapor Smooth + Biocompatible Coating | FDA | 0.2mm |
Source: Independent Prototyping Benchmark Report 2024
When you hold a mirror-polished stainless steel scalpel prototype or a car steering wheel model with a subtle leather texture, the magic of surface finishing goes beyond the technology itself-it’s a crystallization of engineering and aesthetics, and the first breath of a product’s soul.