When SpaceX engineers set ±0.005mm tolerances on recoverable rocket fuel valves, they’re not just chasing precision – they’re balancing the million-dollar cost of failure against the limits of achievable manufacturing.MetaMotion will reveal the exact science behind CNC machining tolerances to help you avoid the over-machining trap and achieve the optimal solution for quality and cost.
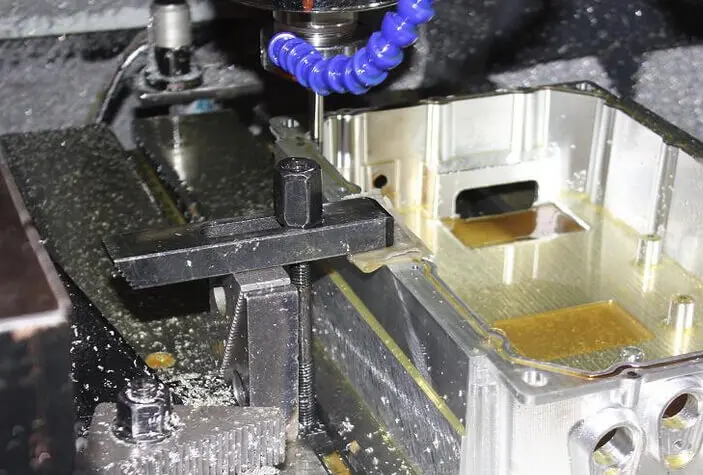
I.The Nature of Tolerance: The “Legal Boundary” of Manufacturing
Strategic Definition of Tolerance
Physical: the range of allowable dimensional variation (upper limit – lower limit)
Economic: the legal boundary between failure risk and manufacturing cost
Case Alert: Tesla’s Battery Cooling Plate was recalled for seal failure due to lack of flatness tolerance, resulting in $1.2M in damages.
International Standard System Analysis
standardized system | Field of application | Core features | Typical Tolerance Grades |
---|---|---|---|
ISO 2768 | General Machinery | 简Simplified labeling, Precision/Medium/Rough | mK grade ±0.1mm |
ASME Y14.5 | Aerospace medical | GD&T Geometric Tolerance System | 0.01mm |
DIN 7167 | European car | system of prioritizing fit tolerances | IT7-IT9 |
Key Insight: Johnson & Johnson Orthopaedic Implants adopts ASME Y14.5 standard to control the tolerance of bone nail thread median diameter to 0.002mm, which reduces postoperative loosening rate by 90%.
II. Tolerance types: four dimensions of precise control
1. Dimensional tolerances: linear boundary guards
Bidirectional symmetric tolerance: ±0.05mm (for non-matching surfaces)
Unidirectional tolerance: +0.00/-0.03mm (shaft-hole mating scenarios)
Limit tolerance: ∅10.2~10.5mm (rough functional parts)
2. Geometric Tolerance: Nuclear Weapons for Precision Control
# GD&T five core symbols
sign | name | control target | Application Cases |
---|---|---|---|
⌖ | positional degree | Hole Group Positioning | Engine Block Bolt Holes |
◎ | concentricity | rotational axis symmetry | turbine journal |
┴ | perpendicularity | Assembly surface relationship | Machine tool guideways |
〱 | flatness | surface flatness | Sealing Flanges |
↗ | circular jump | Rotational accuracy | bearing position |
3. Material properties compensation tolerance
Thermal expansion compensation: Aluminum alloy parts are marked with the tolerance under the ambient temperature of 23±2℃.
Stress deformation warning: Thin-walled parts (<3mm) need to be marked with the clamping deformation tolerance.
III.The accuracy level of practical decoding: from the workshop to the laboratory
CNC machining accuracy pyramid
Accuracy Class | standard tolerance | Applicable Processes | Economic cost index |
---|---|---|---|
medical grade | ±0.005mm | 5-axis mirror milling | $$$$$ |
aviation grade | ±0.01mm | High-speed hard milling + liquid nitrogen cooling | $$$$ |
automotive grade | ±0.03mm | Three-axis finishing | $$$ |
industrial grade | ±0.1mm | General Milling | $$ |
Failure case: a drone manufacturer marked IT5 tolerance (±0.005mm) on the motor mount, resulting in an 8-fold increase in the cost of a single piece, which was later optimized to IT8 (±0.03mm) to meet functional requirements.
Material-Tolerance Matching Matrix
makings | practicable tolerance | Ultimate Challenge | risk of failure |
---|---|---|---|
Aluminum Alloy 6061 | ±0.01mm | Deep cavity machining ±0.03mm | Tool chatter leads to overshoot |
Stainless Steel 316 | ±0.02mm | Thin-walled parts ±0.05mm | Accumulated heat distortion error |
Titanium alloy TC4 | ±0.015mm | Microporous ∅0.3mm±0.005mm | Cutter chipping |
PEEK | ±0.03mm | Thin wall 0.5mm±0.02mm | Elastic Response Error |
IV. The Minefield of Cost Bursts: The Deadly Trap of Excessive Tolerances
Exponential Cost Growth with Tight Tolerances
# Automotive sensor housing tolerance cost model
Tolerance requirements | process solution | unit cost | Increase relative to baseline |
---|---|---|---|
±0.1mm | Conventional 3-axis milling | $18 | standard of reference |
±0.05mm | High-speed precision milling | $42 | 133%↑ |
±0.02mm | 5-axis machine + on-machine testing | $120 | 567%↑ |
±0.01mm | Coordinate grinder | $350 | 1844%↑ |
Four principles of reasonable tolerance setting
Functional priority: sealing surfaces need flatness of 0.01mm, non-matching surfaces are relaxed to 0.1mm
Process matching: 30% relaxation of tolerance for cavities with a depth-to-diameter ratio of >5
Measurement accessibility: Avoid marking tolerances lower than the precision of CMM (0.001mm)
Cost alert: every 1 level of tolerance upgrade, the cost of increasing by 50-200%
Classical case: Apple MacBook Unibody shell will be Non-critical surface tolerance from ± 0.05mm relaxed to ± 0.1mm, annual savings in manufacturing costs $ 2.3M
V. GD&T Practice: Geometric Tolerance’s Cost Reduction Revolution
Positional tolerance instead of dimensional chain
Traditional labeling: 3 dimensional tolerance stacked cumulative error ± 0.15mm
GD&T labeling: position degree ⌖ 0.1mm A|B|C direct control of the hole group positioning
Benefits: 40% increase in the pass rate, 70% reduction in inspection time
Benchmarking system to build the rule of law
Primary datum (A): maximum contact surface (clamping positioning surface)
Secondary datum (B): longest guiding feature
Third datum (C): anti-rotation feature
Application: Boeing wing rib fixture datum design, 35% increase in assembly efficiency
VI.Intelligent Tolerance Optimization System
AI Tolerance Assignment Engine
Siemens Tolerancing Advisor:
Learns 100,000 assembly mating data
Automatically optimizes the tolerance chain (22% cost reduction)
Tolerance Virtual Verification
ANSYS Tolerance Analysis:
Monte Carlo simulation of millions of assemblies
Predicts scrap rate > 99% accuracy
Blockchain tolerance traceability
Digital fingerprints generated for each feature:
Machine tool accuracy certificates
Ambient temperature and humidity records
Tool wear compensation values
As ASME Chief Expert Dr. Peterson says, “Tolerance is a contract between the designer and the fabricator – sensible tolerance is wisdom that honors the limits of manufacturing, not the vanity of accuracy.” When you’re marking tolerances for the next generation of artificial satellite mounts, behind every ±0.001mm is a precise trade-off between the cost and reliability of space exploration.