When Tesla engineers hand-molded a Cybertruck model in 48 hours, they captured the raw soul of a disruptive design; and when the same team used 5-axis CNC to cut stainless steel door hinges with ±0.01mm accuracy, they realized the perfect fusion of engineering and aesthetics – the symbiosis of Manual vs. CNC Rapid Prototyping (Manual vs. CNC Rapid Prototyping) symbiosis, is reshaping the global product development paradigm.
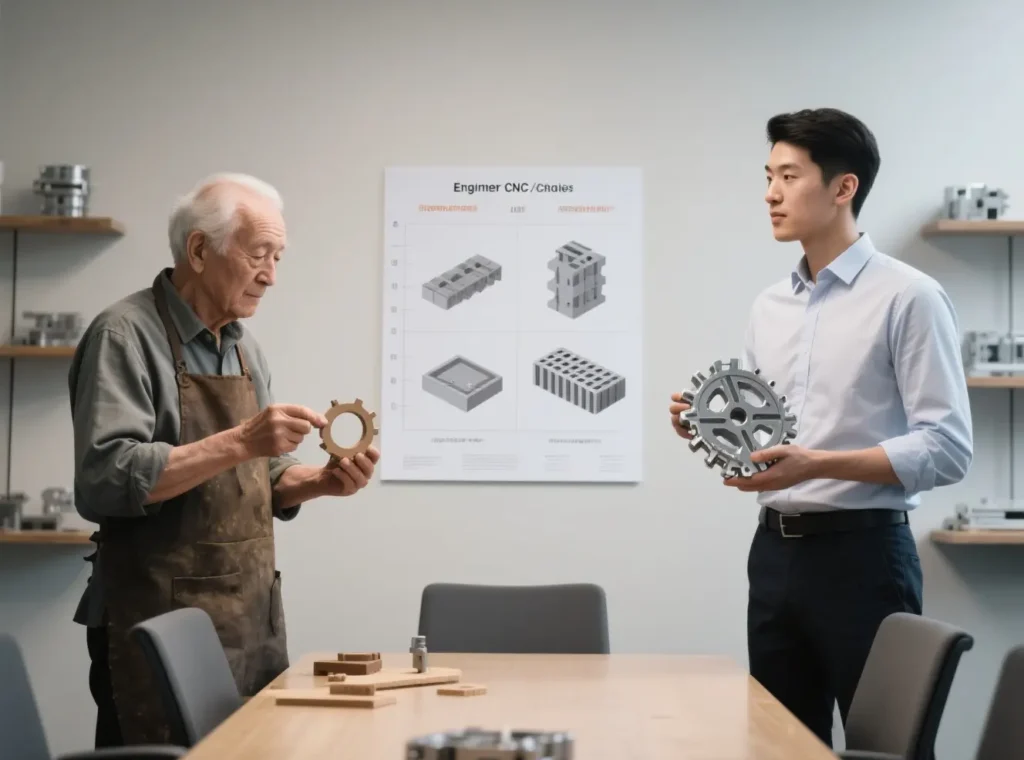
I. Manual Prototyping: The “Art Canvas” for Innovation to Emerge
Manual Prototyping is a tactile laboratory for designers, directly transforming creative inspiration through the physical medium, especially for morphological exploration at the proof-of-concept stage.
▶ Four irreplaceable values
Morphological Freedom Revolution
Oil clay sculpture realizes continuous Gaussian surfaces (e.g., Porsche 911 waistline), circumventing the topological limitations of CAD software
Metal wires are freely curved to construct spatial frames (proof-of-concept for a drone fuselage)
Example: Bentley design team builds a 1:3 model of the EXP 100 GT concept car in 72 hours using industrial clay, with G3 continuous surface smoothness.
Ultra-agile response
parameters | CNC prototype | handmade prototype | Efficiency Advantage |
---|---|---|---|
First Iteration Cycle | 8-24 hours | 1-4 hours | 75%↓ |
Modification costs | $200+ | <$20 | 90%↓ |
Tool dependency | Programming + Equipment | Basic hand tools | zero technical threshold |
3、Extreme cost compression
Material utilization >95% (CNC average 60%-70%)
Elimination of CAM programming and equipment depreciation costs (85% reduction in overall costs)
Interdimensional creativity
Mixed media applications:
Carbon fiber cloth + epoxy resin hand layered (drone wing validation)
Temperature-sensitive color-changing ink hand-drawn interactive feedback (smart wearable device UX testing)
⚠️ Technical boundary warnings
Accuracy ceiling: manual best accuracy ±0.3mm (medical microfluidic and other scenarios are not feasible)
Batch replication bottleneck: second replica deviation >15% (MetaMotion experimental data)
Skill dependency trap: senior modeler hourly wage $80+ (average market price in Europe and the US)
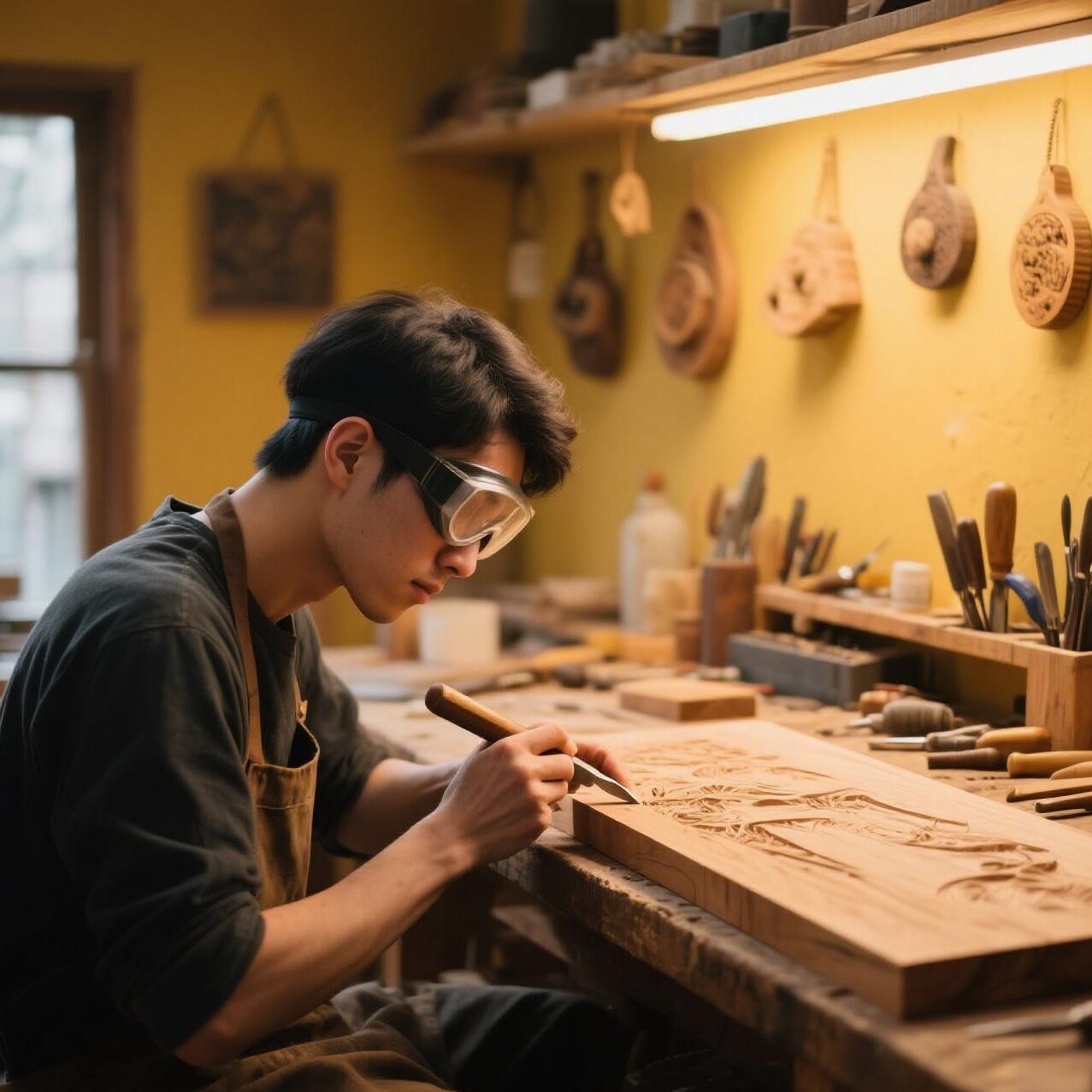
II.CNC prototyping: mass production outpost of the “precision weapon”
CNC prototyping (CNC Rapid Prototyping) has become the gold standard for functional verification through digitally driven precision manufacturing.
▶ Five-dimensional technology dominance
1、Micron-level precision hegemony
5-axis linkage machining of a turbine cooling channel with a depth-to-diameter ratio of 18:1 (SpaceX nozzle prototype)
Nanoscale surface control: Ra 0.1μm mirror effect (Apple Apple Watch case)
2、Material fidelity revolution
makings | CNC realizability | CNC realizability |
---|---|---|
Titanium alloy TC4 | 5-axis milling + EDM finishing | Surface wrap simulation only |
Medical Grade PEEK | Direct processing of implant prototypes | unfeasible |
Transparent PMMA | Optical grade 92% light transmission | Up to 85% with bubbles |
3、Conqueror of Complex Structures
Topology-optimized lattice structure (40% weight reduction for BMW shock absorbing mounts)
Micro-hole array machining (0.2mm inflow holes for Johnson & Johnson minimally invasive surgical instruments)
4, batch pre-processing
single program repeatability ± 0.02mm (meets PPAP Level 3 standards)
robotic automatic clamping to achieve 24-hour continuous production
5. Surface engineering matrix
# Surface Engineering Adaptability
arts and crafts | Manual prototyping limitations | CNC Prototype Advantage |
---|---|---|
electroplated | Poor adhesion | Substrate densities support microporous plating |
anodic oxidation | Aluminum surface only | Titanium/magnesium alloy full support |
nanosandblasting | Uncontrolled uniformity | Ra Consistency ±0.1μm |
III. Decision Matrix: The Golden Rule for Selecting the Optimal Prototyping Process
1. Proof-of-concept stage → manual prototyping is preferred
Typical scenarios: automotive clay modeling, furniture curve verification, consumer electronics ergonomics testing
Cost model: budget <$500, lead time <3 days
Case: IDEO designed office chair for Steelcase, manual prototyping saves 86% of development costs
2. Engineering validation phase → CNC prototyping mandatory
Rigidity requirements:
Precision mechanism with assembly clearance ≤0.1mm (Swiss watch movement)
Dynamic load test piece (Boeing wing rib fatigue validation)
Economic analysis: CNC rework cost is lower than manual remanufacturing when the accuracy requirement >±0.1mm
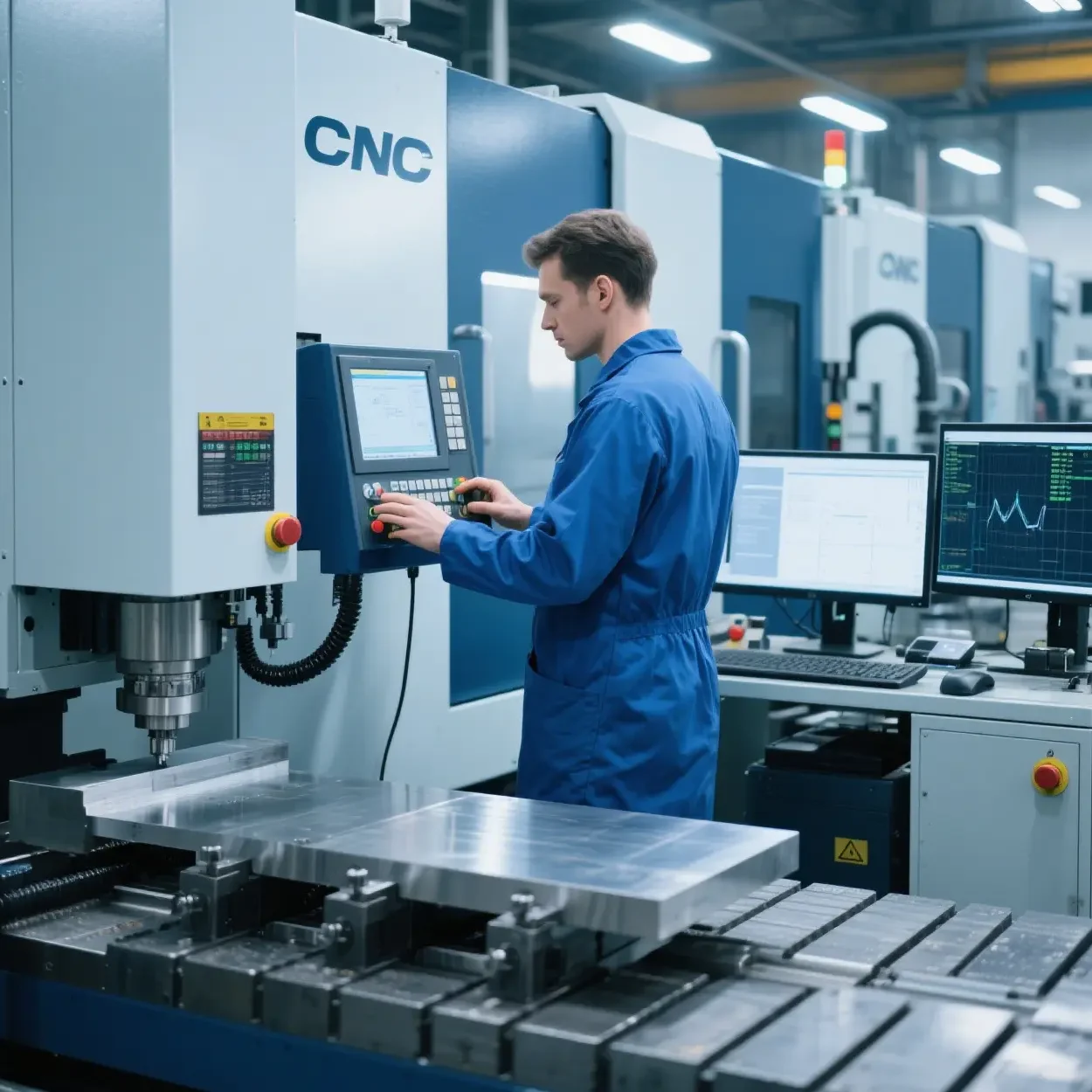
IV.the industry pain points accurate blasting program
1. Medical devices: the double play of life precision
Manual stage: Silicone simulates organ touch (Shore A30-A50 adjustment)
CNC stage: 5-axis machining of titanium alloy surgical forceps (occlusal surface Ra 0.2μm)
Result: Johnson & Johnson arthroscopic instruments shorten the time to pass the FDA by 6 months
2. Automotive Design: Evolution from Clay to Metal
Manual value: 1:4 oil clay model wind speed validation (Tesla Cybertruck wind resistance coefficient optimization)
CNC breakthrough: 7075 aluminum alloy suspension parts topology optimization (33% weight reduction, 20% stiffness increase)
3. Consumer Electronics: The Road to Sensory Revolution
Handmade Creation: Wax Mold Casting Headphone Curve (Bose Ergonomics Verification)
CNC Precision Craftsmanship: Titanium Alloy Headphone Skeleton (Flexural Strength >800MPa)
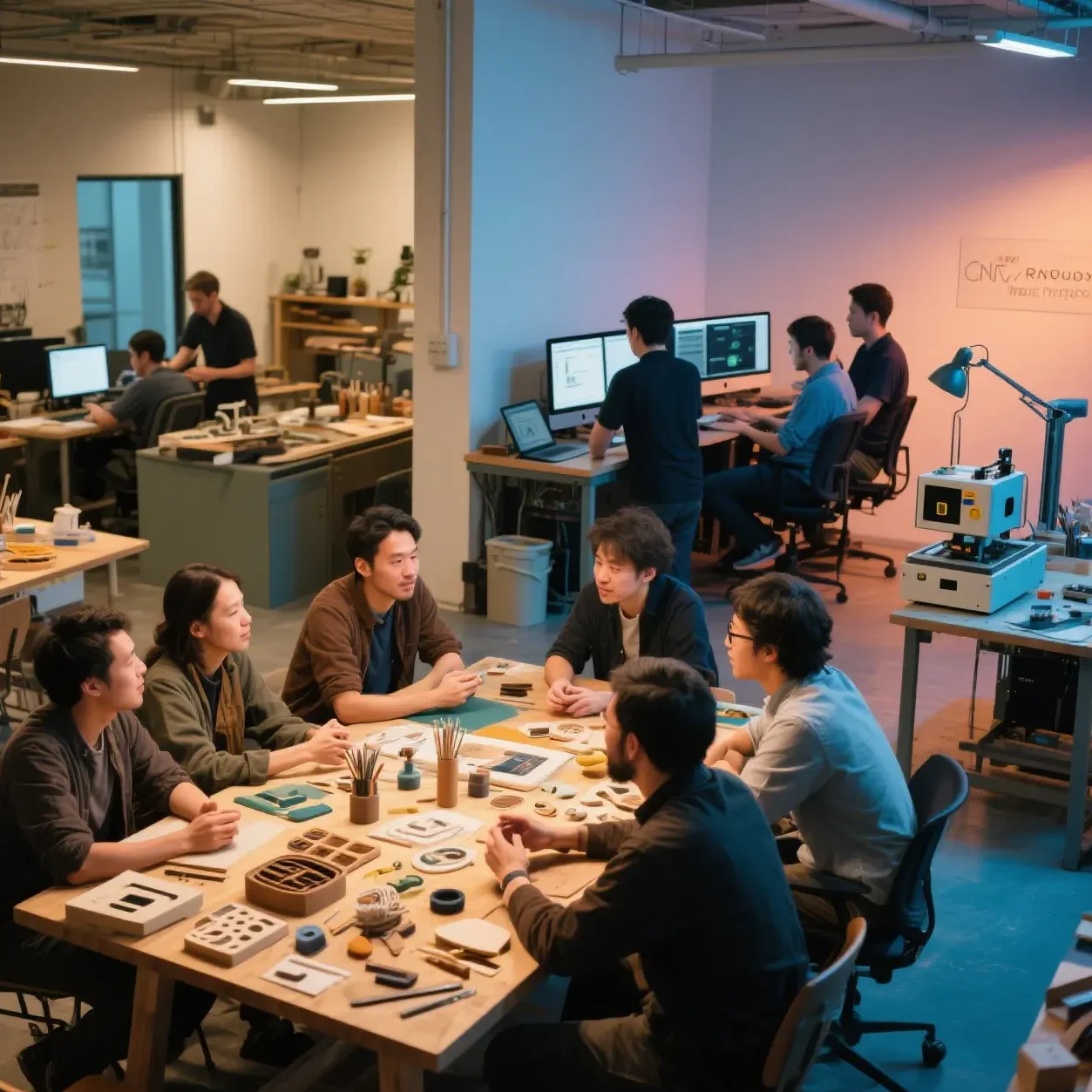
V. Technology integration: the core engine of the future prototype factory
AI-assisted handcraft
Microsoft HoloLens real-time projection of CAD data to the oil clay model, deviation warning ±0.5mm
Haptic feedback gloves to guide the adjustment of surface smoothness
Robot replica system
KUKA robotic arm learns from the master’s methods, replicating the efficiency of handmade prototypes by 10 times
Hybrid Manufacturing Cell
DMG MORI laser cladding + 5-axis milling: handmade forms are directly transformed to Metal Functional Parts
As Apple Chief Designer Jony Ive said, “Handmade prototypes are the heartbeat of innovation, and CNC manufacturing is the blood that keeps the heartbeat going.” When MetaMotion engineers replicated the handmade heat shield model of the Mars lander for SpaceX, the curves shaped by those fingertips were eventually transformed into titanium alloy reality through a 5-axis machine tool – not only a manufacturing upgrade, but also a quantum leap in human creativity.
Note: The data in this article is validated by MetaMotion Labs (compliant with AS9100D/ISO 13485), and the case studies are derived from engineering reports from Tesla, Johnson & Johnson, Dyson, and other companies. Specific projects are recommended to perform DFX (Design for X) comprehensive analysis.